welcome to m/s nitin mechanical works pvt ltd .... our 2nd unit name is m/s ps engineering works
Pipe Machine
Leading manufacturer of PVC pipe machines for HDPE and PVC pipes.
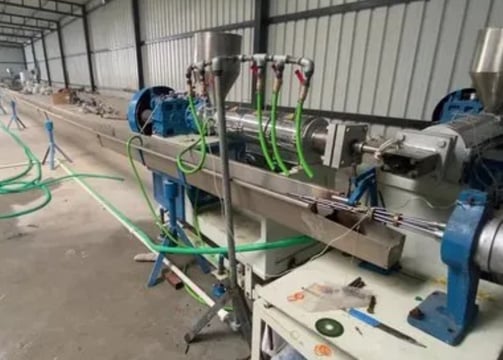
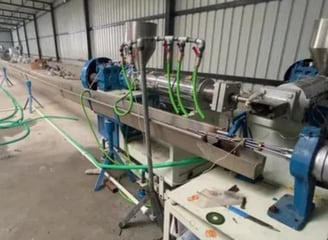
PVC SUCTION HOSE PIPE PLANT
Our PVC suction hose pipe machine is designed for precision and efficiency, enabling the production of flexible and durable suction hoses that meet the diverse demands of various industries.
USES
PVC suction hose pipes are widely used for a variety of applications, including the transportation of water, liquids, and granular materials in agriculture, construction, and industrial settings. They are known for their flexibility, lightweight design, and resistance to abrasion, making them ideal for suction and discharge tasks in various environments.
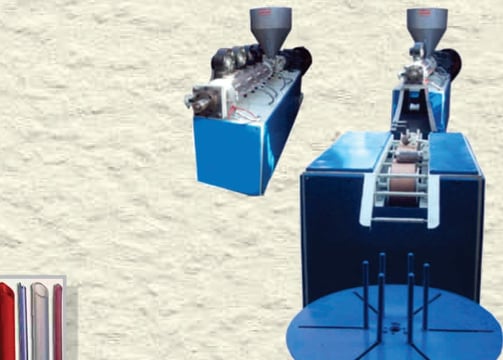
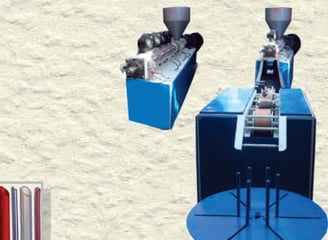
PVC GARDEN HOSE PIPE MACHINE
The PVC garden hose pipe machine is engineered to produce high-quality and durable garden hoses, providing homeowners and landscapers with reliable solutions for efficient watering and irrigation in gardens and lawns.
USES
Garden hose pipes are versatile tools commonly used for a variety of tasks, including watering plants and lawns, washing cars, cleaning outdoor surfaces, and filling swimming pools. Their flexibility and portability make them essential for both residential and commercial gardening and landscaping needs.
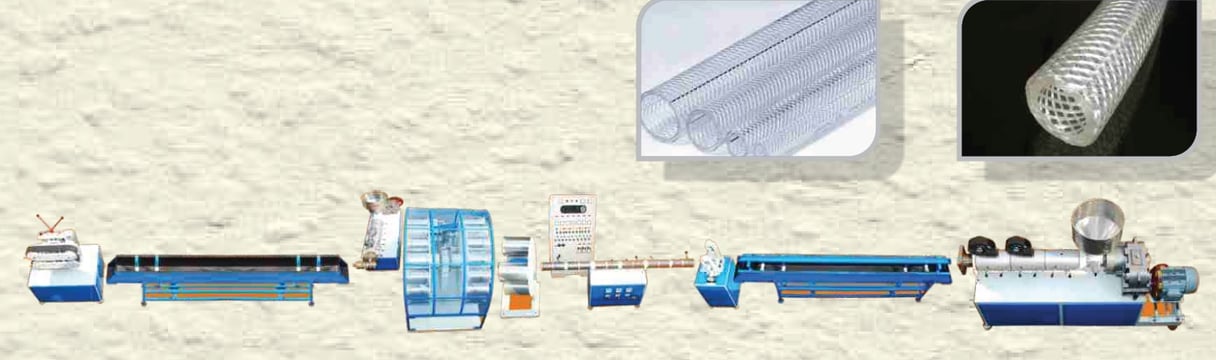
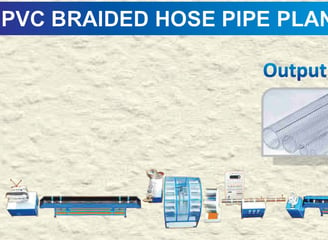
PVC BRAIDED HOSE PIPE MACHINE
The PVC braided hose pipe machine is expertly designed to manufacture strong and flexible braided hoses, ensuring optimal performance for various applications in industries such as agriculture, construction, and fluid transport.
USES
PVC braided hose pipes are utilized in numerous applications, including water supply, irrigation systems, air and gas transfer, chemical handling, and automotive uses, thanks to their durability, flexibility, and resistance to abrasion and pressure
→
→
→
→
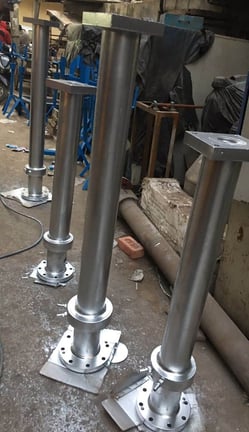
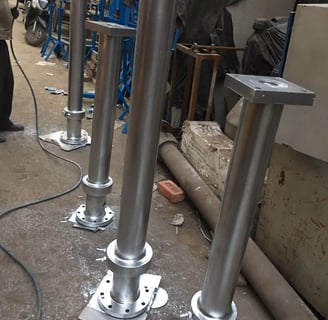
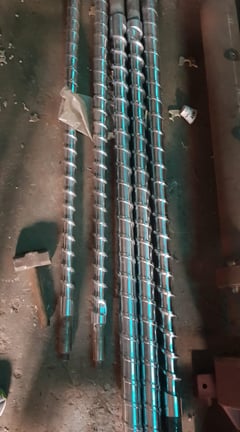
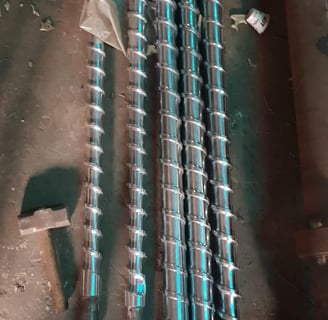
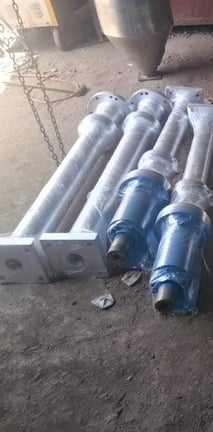
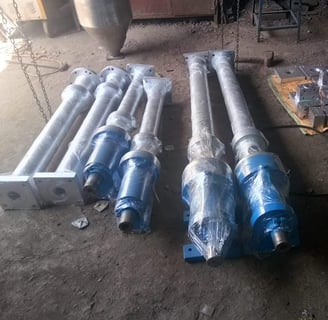
SCREW AND BARRELS FOR MAKING PVC AND HDPE PIPE
Our screw barrels are crafted from EN41B material and are precisely nitrided and hard chrome plated, ensuring exceptional durability and performance in the production of PVC and HDPE pipes.
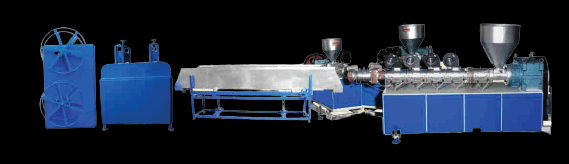
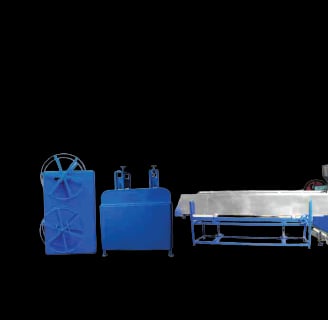
LD KRISHI HOSE PIPE MACHINE
LD KISAN PIPE MACHINE
The LD Kisan pipe machine is engineered for optimal efficiency and precision, delivering high-quality low-density polyethylene (LDPE) pipes that cater to the diverse needs of agricultural irrigation and water management systems.
USES
LD Kisan pipes are ideal for agricultural irrigation, providing farmers with a reliable and efficient solution for delivering water to crops while minimizing wastage and ensuring optimal growth.
HDPE SINGLE WALL CORRUGATED PIPE MACHINE
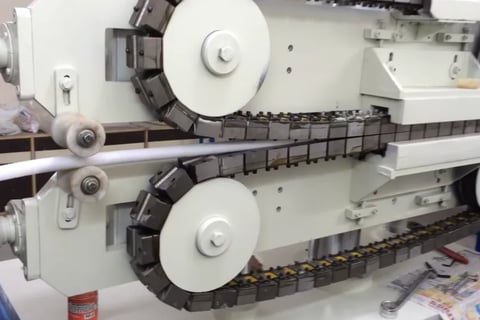
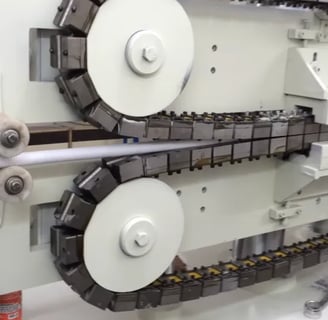
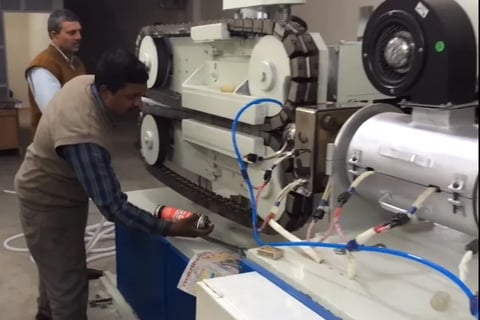
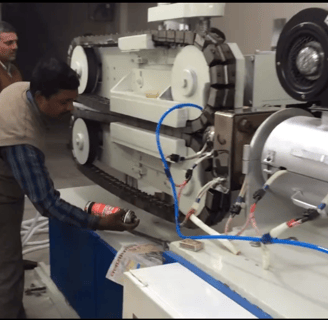
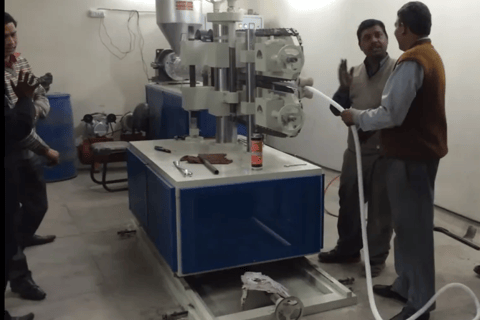
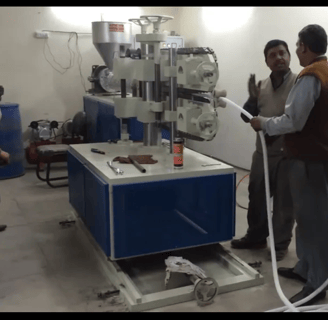
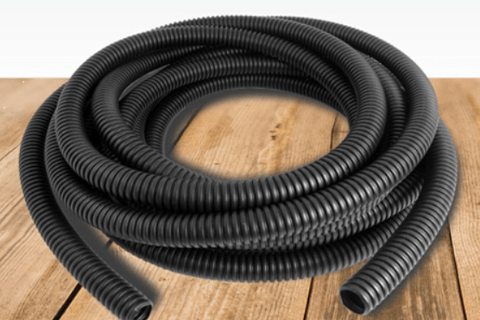
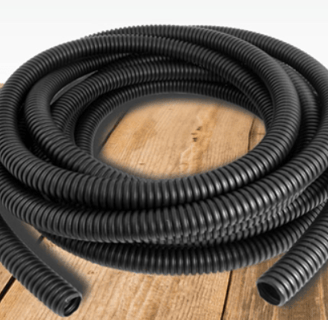
The HDPE corrugated pipe machine produces durable, flexible, and lightweight pipes made from HDPE. These pipes are known for their resistance to corrosion, chemicals, and environmental stress, making them suitable for underground installation.
Extruder:
The primary component that melts and processes the HDPE plastic material. The extruder feeds the molten plastic into the die.
Die:
The die shapes the molten HDPE into the desired pipe profile. In the case of corrugated pipes, it creates the specific corrugation shape that provides strength and flexibility.
Corrugating Unit:
This section of the machine forms the corrugations in the pipe. It typically has a set of rollers that shape the extruded material as it cools.
Cooling System:
After the pipe is extruded and formed, it is cooled to solidify the material. This can be achieved using air or water cooling systems.
Cutting Unit:
This part of the machine trims the length of the finished pipe to the desired specifications.
Control System:
Modern machines have computerized control systems that allow for adjustments and monitoring throughout the production process, ensuring consistency and quality of the output.
Applications
Drainage Systems: Used in road, trench, and surface drainage systems.
Stormwater Management: Effective in managing stormwater runoff and preventing flooding.
Sewage and Wastewater Systems: Suitable for underground sewage systems due to its resistance to chemicals and corrosion.
Irrigation Systems: Widely used in agricultural applications for water distribution.
Telecommunication and Electrical Conduits: Used as protective conduits for cables and pipes.
HIGH SPEED MIXTURE
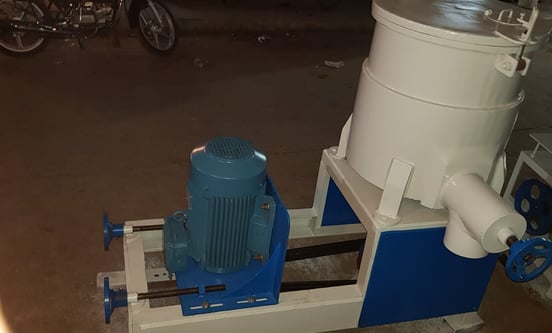
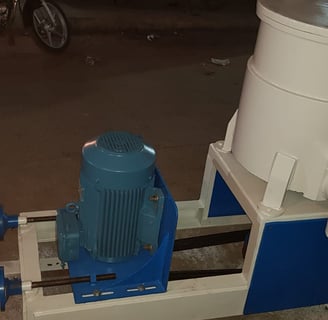
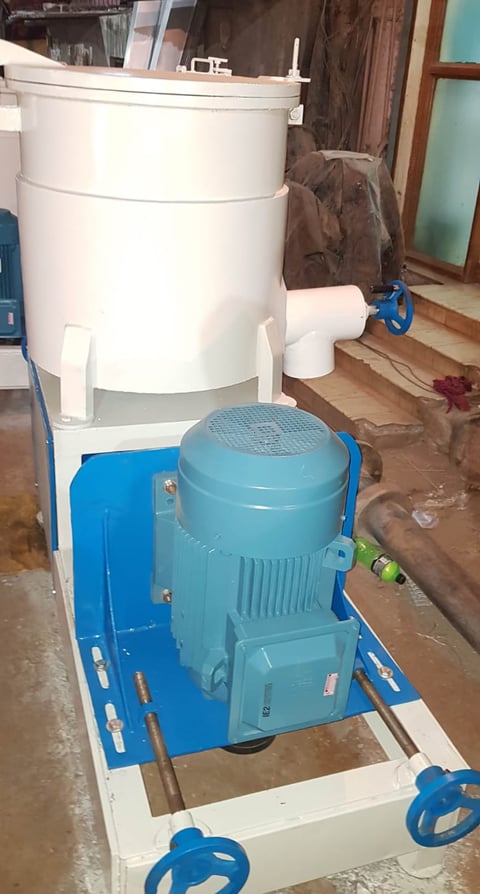
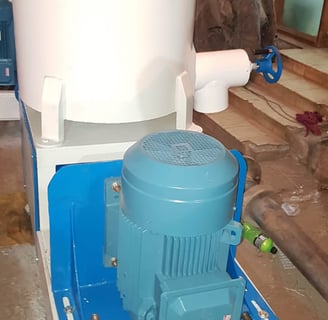
Function: High-speed mixers are used to blend PVC resin with other materials thoroughly. This ensures a homogenous mixture that can be processed effectively in subsequent manufacturing steps. The mixing process is essential for achieving the desired properties of the final PVC product, such as color, strength, and flexibility.
Key Components
Mixing Chamber:
This is where the ingredients are loaded and mixed. It usually has a specific design that promotes efficient mixing.
Mixing Blades:
High-speed mixing blades are used to agitate the mixture at high speeds. These blades create shear forces that break down agglomerates and ensure uniform dispersion of additives.
Feeding System:
The machine will often include a feeding system for adding raw materials, such as PVC resin, stabilizers, plasticizers, fillers, and colorants, into the mixing chamber.
Heating/Cooling Systems:
Some high-speed mixers may include heating or cooling capabilities to maintain the desired temperature during processing, as the mixing process can generate heat.
Control Panel:
Modern high-speed mixers often feature digital control panels that allow operators to monitor and adjust mixing parameters such as speed, time, and temperature.
Discharge System:
After mixing, the blended material is discharged for further processing. This could involve transporting the mixture to an extruder or molding machine.
Advantages
Efficiency: High-speed mixers significantly reduce the mixing time compared to traditional mixing methods, increasing overall production efficiency.
Uniformity: They ensure thorough blending of materials, leading to consistent quality in the finished products.
Versatility: Can handle a variety of PVC formulations and additives, making them suitable for different PVC products.
Energy Savings: Advanced models are designed for optimal energy efficiency during operation.
Reduced Labor: Automated controls reduce the need for manual intervention, allowing for a more streamlined process.
Applications
PVC Pipe Production: Used to create the base compound for PVC pipes, ensuring consistent quality and performance.
Sheet and Film Production: Essential in producing PVC sheets, films, and other flat products with specific characteristics.
Profiles and Molded Items: Utilized in the creation of various profiles and molded PVC products for construction and manufacturing industries.
Plasticizer and Stabilizer Mixing: Blends various additives to enhance the properties of PVC, such as impact resistance or thermal stability.
RIBBON BLENDER / SLOW SPEED MIXTURE FOR PVC
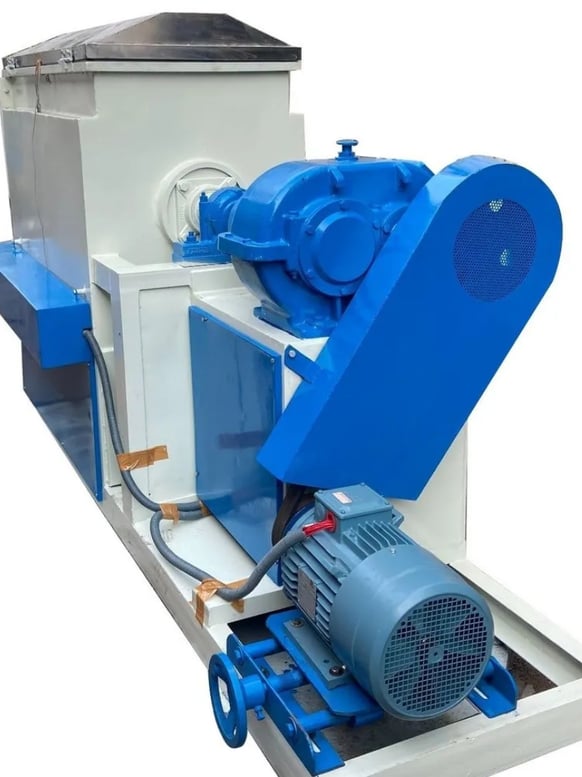
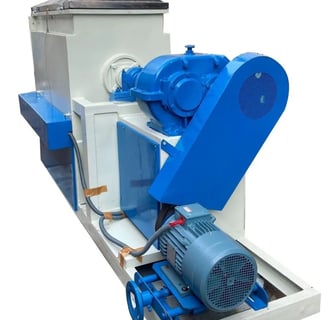
A ribbon blender is a type of industrial mixing equipment commonly used for blending dry powders and granular materials, including PVC (polyvinyl chloride) compounds. Ribbon blenders are particularly effective for producing homogeneous mixtures of PVC resin and various additives, such as plasticizers, stabilizers, fillers, and colorants. Below is an overview of ribbon blenders, focusing on their design, function, advantages, and applications in PVC processing.
Overview
Function: The primary function of a ribbon blender is to mix PVC materials thoroughly. The blender creates a uniform mixture by moving the materials through the mixing chamber using a ribbon-like agitator that operates within a U-shaped trough.
Key Components
Mixing Chamber:
The trough where the ingredients are loaded for mixing. It is typically U-shaped to allow for effective mixing.
Ribbon Agitator:
The ribbon-shaped blades rotate around the axis of the trough, pushing the materials toward the center and then back out towards the walls, facilitating a thorough mixing action.
Drive System:
An electric motor powers the ribbon agitator. The speed can often be adjusted to achieve the desired mixing consistency.
Discharge Outlet:
This is located at one end of the trough and is used to remove the mixed product at the end of the mixing process.
Control Panel:
Ribbon blenders may be equipped with control panels that allow operators to monitor and adjust mixing times and speeds.
Advantages
Uniform Mixing: Ribbon blenders provide excellent blending performance, ensuring that all components of the PVC mixture are evenly distributed.
Gentle Processing: The design of the ribbon blender minimizes shear forces, making it suitable for mixing delicate materials without damaging them.
Versatility: Able to handle a wide range of materials and additives, making it suitable for various PVC formulations and products.
Ease of Cleaning: Many ribbon blenders are designed for easy disassembly, making cleaning and maintenance straightforward.
Scalability: Available in various sizes, ribbon blenders can be used for both small batch sizes and large-scale production.
Applications
PVC Compound Production: Used in the preparation of PVC compounds for pipes, profiles, films, and other products, ensuring uniform properties in the final products.
Mixing Additives: Effective for blending various additives, such as stabilizers, plasticizers, fillers, and lubricants, that enhance the performance and processing characteristics of PVC.
Food and Pharmaceutical Industries: Although primarily used in the plastics industry, ribbon blenders are also used in food and pharmaceutical applications for mixing powders and granules.
Building and Construction Materials: Used to mix PVC materials for products like flooring, wall coverings, and roofing membranes.
Conclusion
Ribbon blenders are valuable equipment in the processing of PVC materials, providing efficient and effective mixing solutions. Their ability to create homogeneous mixtures of PVC resin and additives makes them essential in producing high-quality PVC products. Their versatile design, ease of maintenance, and gentle mixing action make them ideal for a variety of applications across different industries.
WASTE GRINDER FOR PVC/HDPE/LD
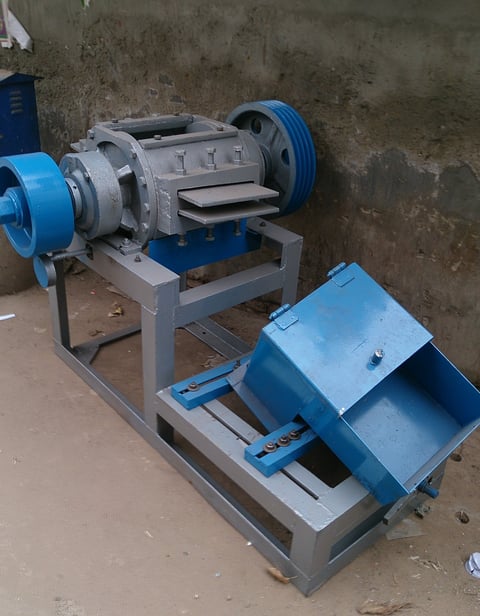
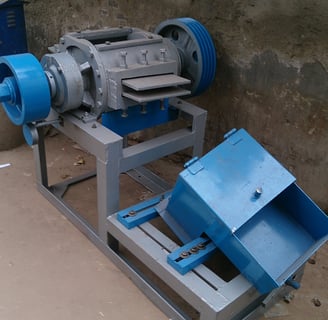
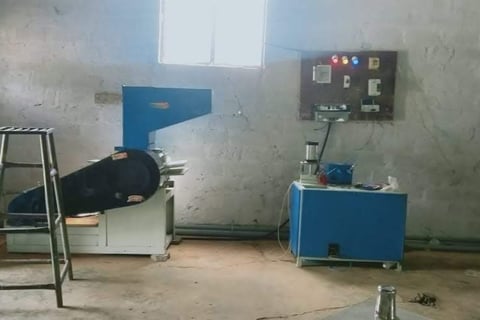
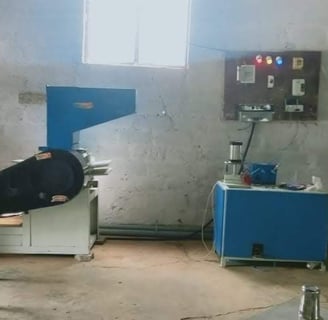
A waste grinder machine for PVC (Polyvinyl Chloride) and HDPE (High-Density Polyethylene) is a specialized piece of equipment designed to efficiently grind and recycle plastic waste materials. This type of machine is essential in the plastic processing industry, as it allows manufacturers to reuse scrap materials, reducing waste and production costs. Here’s an overview of the waste grinder machine, its features, benefits, and applications:
Overview
Function: The main function of a waste grinder machine is to reduce the size of plastic waste, including scrap pieces, off-cuts, and defective products made from PVC and HDPE, into smaller, manageable particles or flakes. This grinding process makes it easier to recycle the materials for reuse in the production of new plastic products.
Key Components
Feeding System:
The feeding system is designed to load the plastic waste into the grinder. It can include hoppers or conveyors that allow for continuous feeding of material.
Cutting Mechanism:
The core of the machine consists of sharp blades or knives that are mounted on a rotor. These blades rotate at high speeds to cut and grind the plastic waste into smaller pieces.
Screen Mesh:
Depending on the desired size of the output material, the grinder typically has screens with varying mesh sizes that determine the final particle size. The particles passing through the screen are collected, while those that do not may be further processed.
Motor and Drive System:
A powerful motor drives the rotor and cutting blades, enabling the machine to handle tough plastic materials efficiently.
Discharge System:
Ground plastic particles are expelled from the machine through a discharge outlet, often leading to a collection bin, conveyor, or further processing units.
Control Panel:
Many waste grinders come equipped with control panels that allow operators to monitor and adjust the machine’s settings, such as speed and operating time.
Advantages
Material Recycling: The grinder allows for the recycling of plastic waste, contributing to sustainability and cost savings in production processes.
Efficiency: High-capacity grinders can quickly process large volumes of waste, enhancing operational efficiency.
Versatility: Suitable for various types of plastics, including PVC, HDPE, and others, allowing manufacturers to handle different waste materials within the same machine.
Reduced Waste: By grinding plastic waste, companies can minimize landfill contributions and comply with environmental regulations.
Improved Material Quality: The grinding process can improve the quality of the recycled material, making it usable in creating new products with consistent properties.
Applications
Plastic Manufacturing: Used in plastic processing plants to recycle scrap materials generated during production, such as off-cuts and defective items.
Plastic Recycling Facilities: Waste grinders are essential in recycling centers that process post-consumer plastic waste by grinding it before further processing.
Injection Molding and Extrusion: In injection molding and extrusion operations, waste grinders are utilized to recycle sprues, runners, and defective parts for re-entry into the manufacturing process.
Construction and Building Material Production: Grinded HDPE and PVC can be used in manufacturing new products, including pipes, sheets, and profiles.
Conclusion
A waste grinder machine for PVC and HDPE plays a critical role in the recycling and processing of plastic materials in various industries. By efficiently grinding plastic waste into reusable feedstock, these machines contribute to sustainability efforts while also reducing production costs. Understanding their operation and benefits helps manufacturers optimize waste management practices and enhance their overall production efficiency.
Pipe Machine Manufacturer Services
Specializing in PVC and HDPE pipe machine manufacturing with high-quality products and efficient service.
WHY INDUSTRIAL TOOLS IS NECESSARY
Industrial tools are essential for several reasons:
Efficiency: They help perform tasks more quickly and with less manual effort, increasing productivity in various industrial processes.
Precision: Many tasks require a high degree of accuracy, which industrial tools can provide, leading to better quality in manufacturing and assembly.
Safety: Specialized tools are designed to minimize risks associated with manual labor, reducing injuries and enhancing worker safety.
Durability: Industrial tools are built to withstand harsh environments and heavy use, ensuring they last longer than regular tools.
Versatility: They can be used for a variety of applications, from construction and repair to fabrication and assembly, making them valuable across different industries.
Cost-Effectiveness: Investing in high-quality industrial tools can save money in the long run by reducing labor costs and minimizing waste.
Innovation: The design and development of advanced tools can lead to new processes and techniques, driving innovation within industries.
Overall, industrial tools play a crucial role in enhancing operational efficiency, safety, and quality in various sectors.
WE MAKE SO MANY PIPE MACHINE
It sounds like you are involved in the manufacturing of pipe machines or related equipment. If you’re looking for specific information or assistance regarding pipe machines, such as types of machines, their applications, best practices, maintenance tips, or any other aspect related to your business, please let me know how I can help!
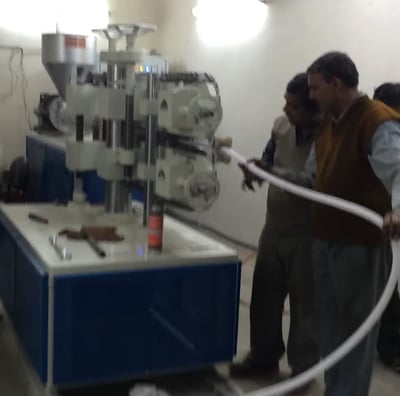
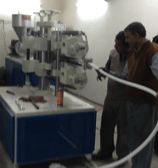
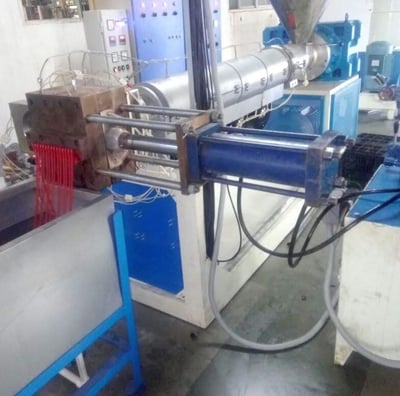
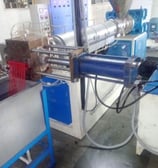
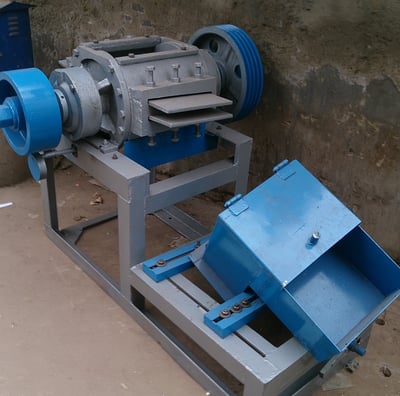
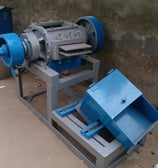
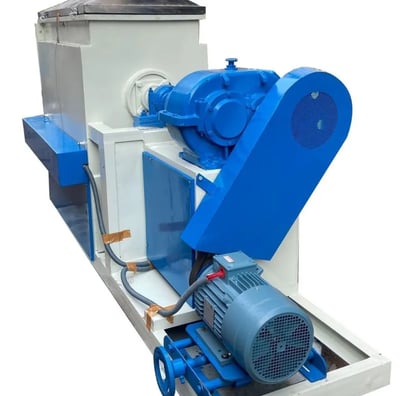
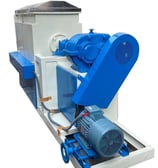
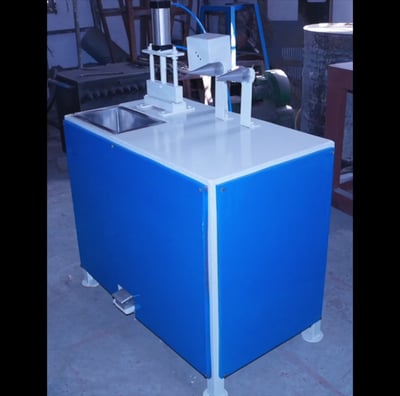
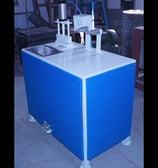
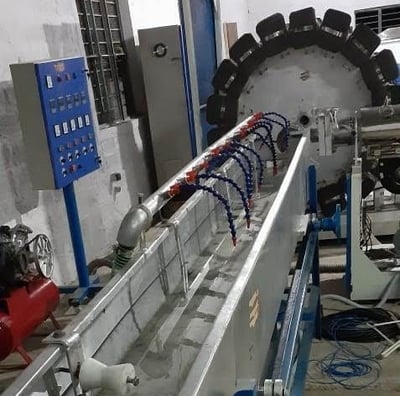
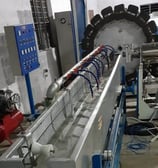